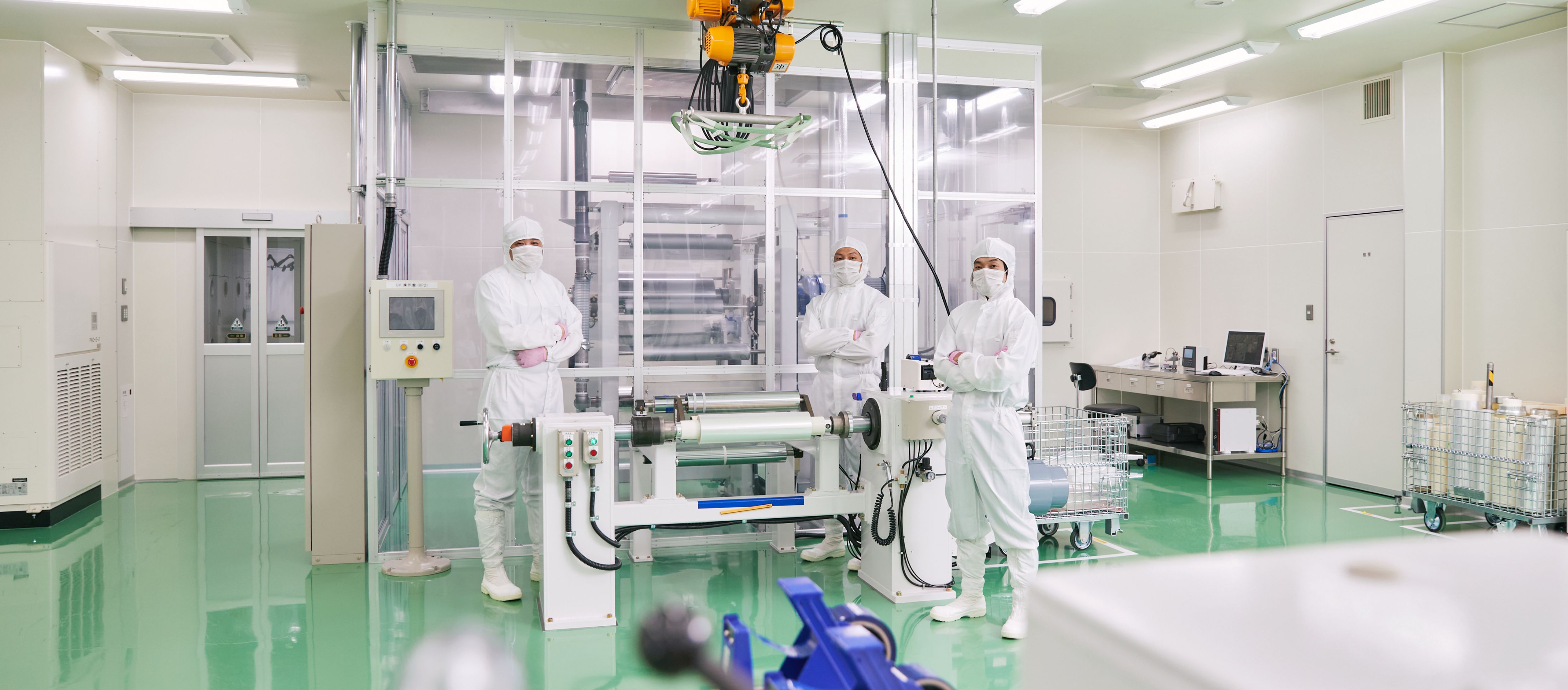
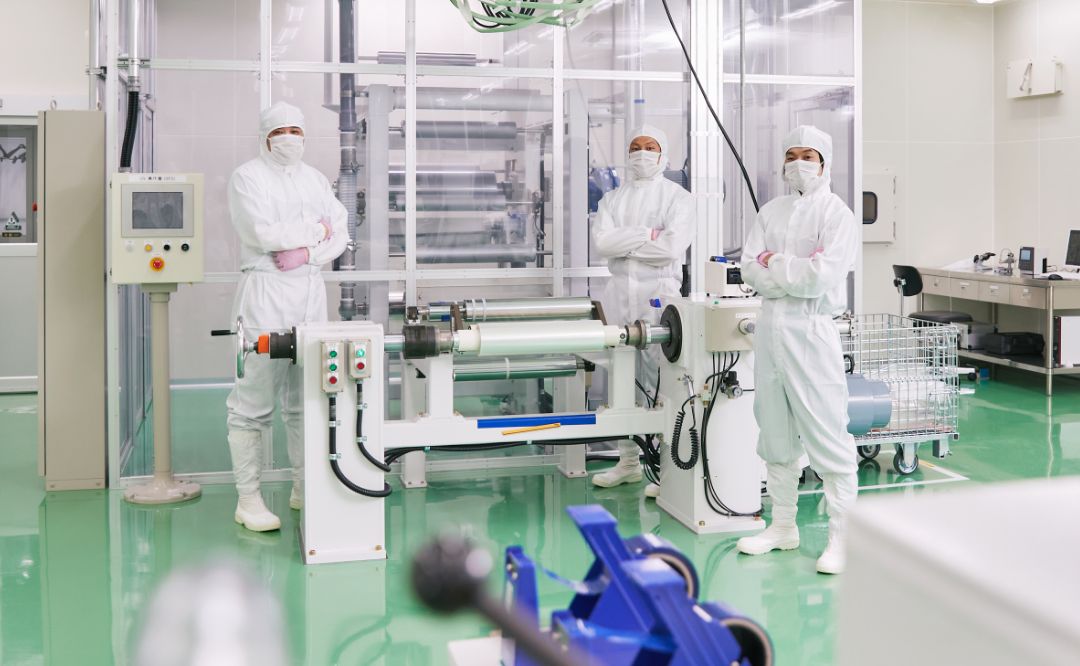
スマートフォン・EVなど
未来産業と社会を支える
プロジェクト。
世界初となる新技術を搭載したコーティングマシンを開発。
プロジェクト | 産業機械 | 研究開発
INTRODUCTION
今ではなくてはならない生活必需品となったスマートフォン。カーボンニュートラルの世界的流れを受け急速に開発が進んでいるEV(電気自動車)。それらに必要不可欠なのがリチウムイオンバッテリーである。世界的に需要が高まっているリチウムイオンバッテリーは、正極材・負極材・セパレータ・電解液で主要構成されている。その中のセパレータに安全性とバッテリー性能を高めるコーティング機械こそ、今回のプロジェクトの中心となる「両面DMコータ」だ。世界最先端の技術であり、世界中から注目を集めるヒット商品の開発ストーリーを追う。
PROJECT MEMBER
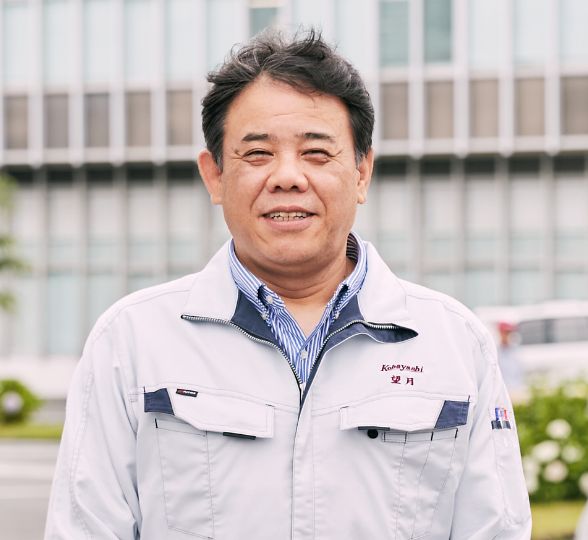
産業研究開発部 望月 章仁
1993年入社 工学部卒
大学で機械工学を学び、人々の生活に役立つモノづくりに関わりたいという想いから小林製作所へ入社。入社以来、研究開発業務に携わり、30年以上のキャリアを持つ。現在は、管理職として各プロジェクトのマネジメントも担う。
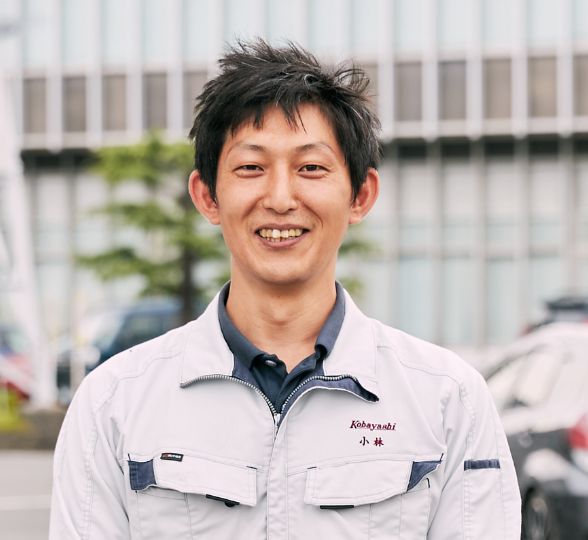
産業研究開発部 小林 秀典
2006年入社 工学部卒
子どもの頃からプラモデルが好きで、モノづくりに興味を持ち、新卒で小林製作所へ入社。1年目は組み立て業務を経験し、2年目から研究開発の業務へ。DMコータ(コーティング機械)の開発を中心に様々なプロジェクトに関わる。
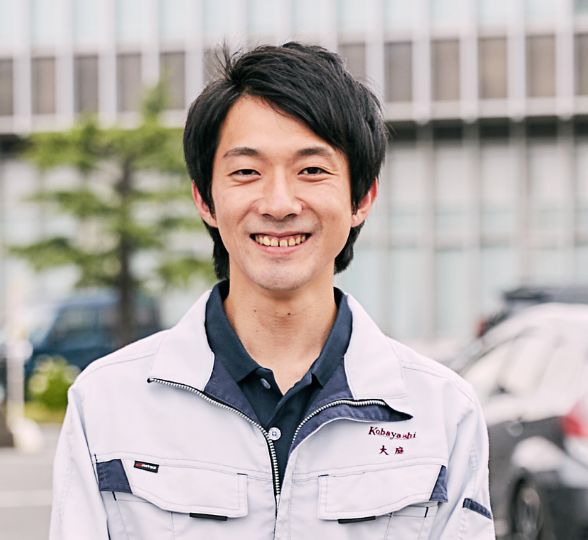
産業研究開発部 大庭 健吾
2013年入社 理工学研究科卒
大学では電気を専門に勉強。機械と電気を組み合わせたモノづくりに興味を持ち、200m級の大型機械をつくっている小林製作所に惹かれ入社。入社後は研究開発部に配属され、現在では流体解析のスペシャリストとして活躍中。
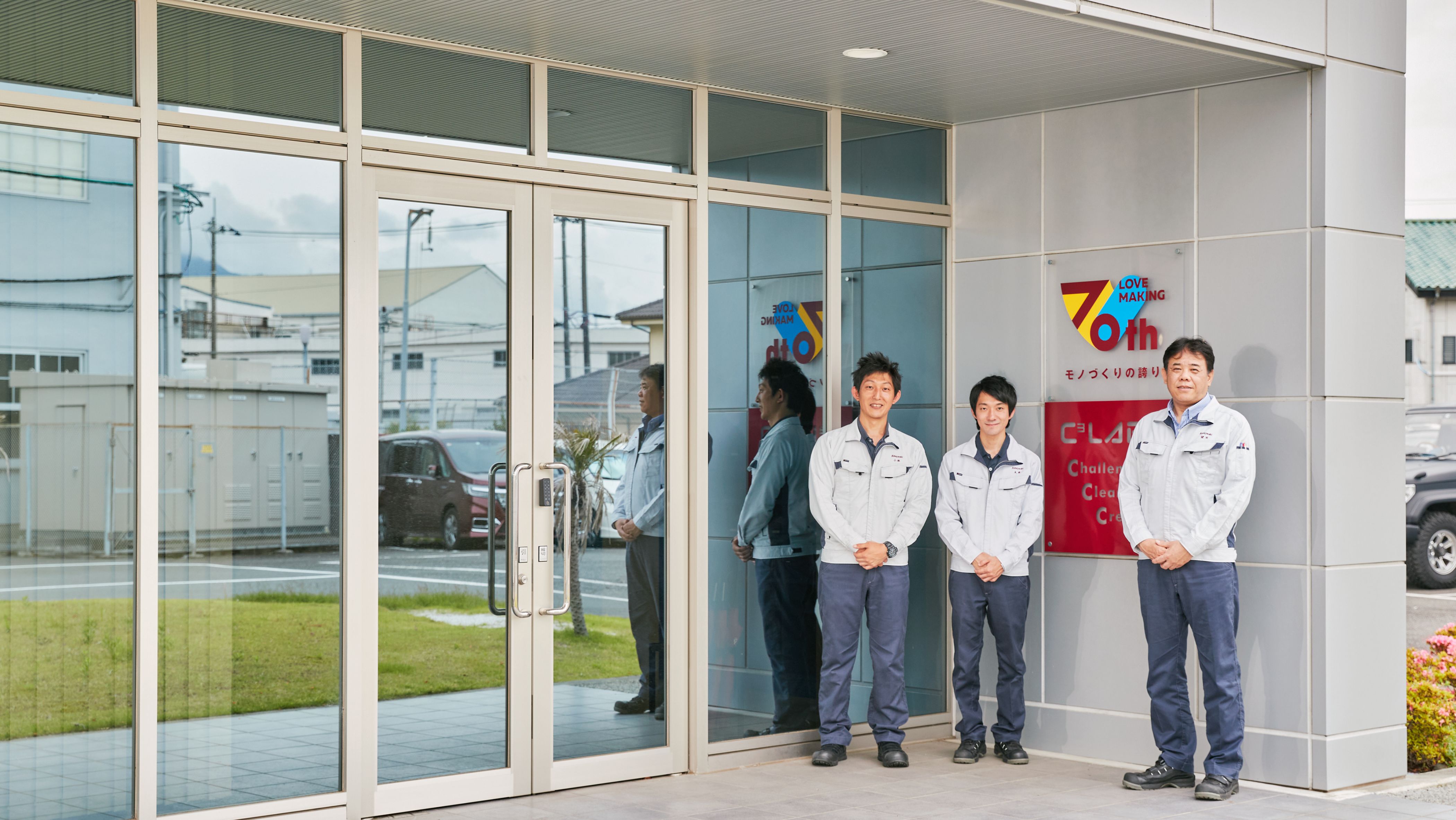
STORY・01
世界初の新技術へのチャレンジ。
前例のない挑戦に立ちはだかる
大きな課題。
2006年から開発をスタートしているDMコータ(ダイレクトメタリングコータ)は、もともとはディスプレイなどの光学用途として用いられるコーティング機械だった。毎年のように改良が進められる中、転機となったのは2012年。韓国の大手有名企業から、スマートフォンやノートパソコンなどに使用されるリチウムイオンバッテリーのコーティング機械としての改良を依頼された。 クライアントからの要望は、生産性の向上。これまでリチウムイオンバッテリーを両面同時コーティングする際は、垂直にフィルムを搬送していた。しかし機械を上に伸ばしていくのには限界がある。水平にフィルムを搬送していくコーテイング機械であれば拡大可能だが、こちらは片面コーティングの機械しか世の中に存在しない。つまり、クライアントの要望を叶えるためには、世界のどこにもない「水平かつ両面にコーティングできる機械」を開発する必要があるということだ。
そこで、研究開発部のメンバーは早速、その世界初となる機械の製品開発に乗り出した。プロジェクトのリーダーを務めるのは、研究開発部で20年のキャリアを持つ望月。望月は当時を振り返りこう語る。「世の中にまだないものをつくるということで、最初は本当に綺麗に両面塗れるのか(コーティングできるか)が心配でした。でもテストを行うと両面コーティングはすぐに成功しました。むしろ大変なのは乾燥のほう。この課題にメンバー全員が頭を悩ませました。」
コーティングを行うフィルムは、コンビニなどで使うレジ袋を想像すると分かりやすい。非常に薄い素材で、風が当たるとバタバタと揺らぐ。しかし、乾燥させるには熱風を吹き付けながら搬送させる必要がある。このとき少しでもフィルムが揺らぐと、シワができてしまい製品にならなくなる。何度も繰り返しテストを行うが、一向に上手くいかない。メンバーに焦りの色が見えはじめた。
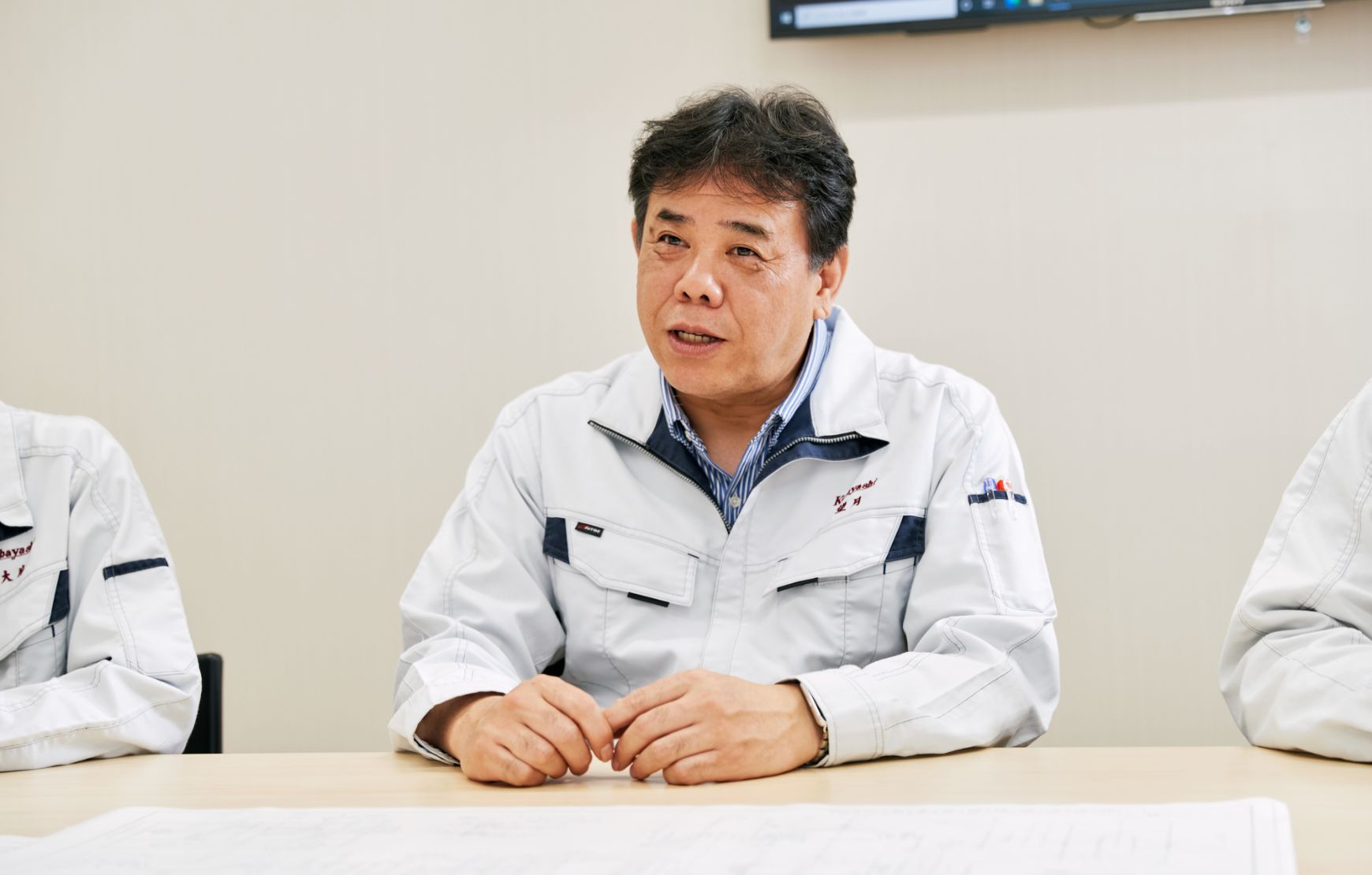
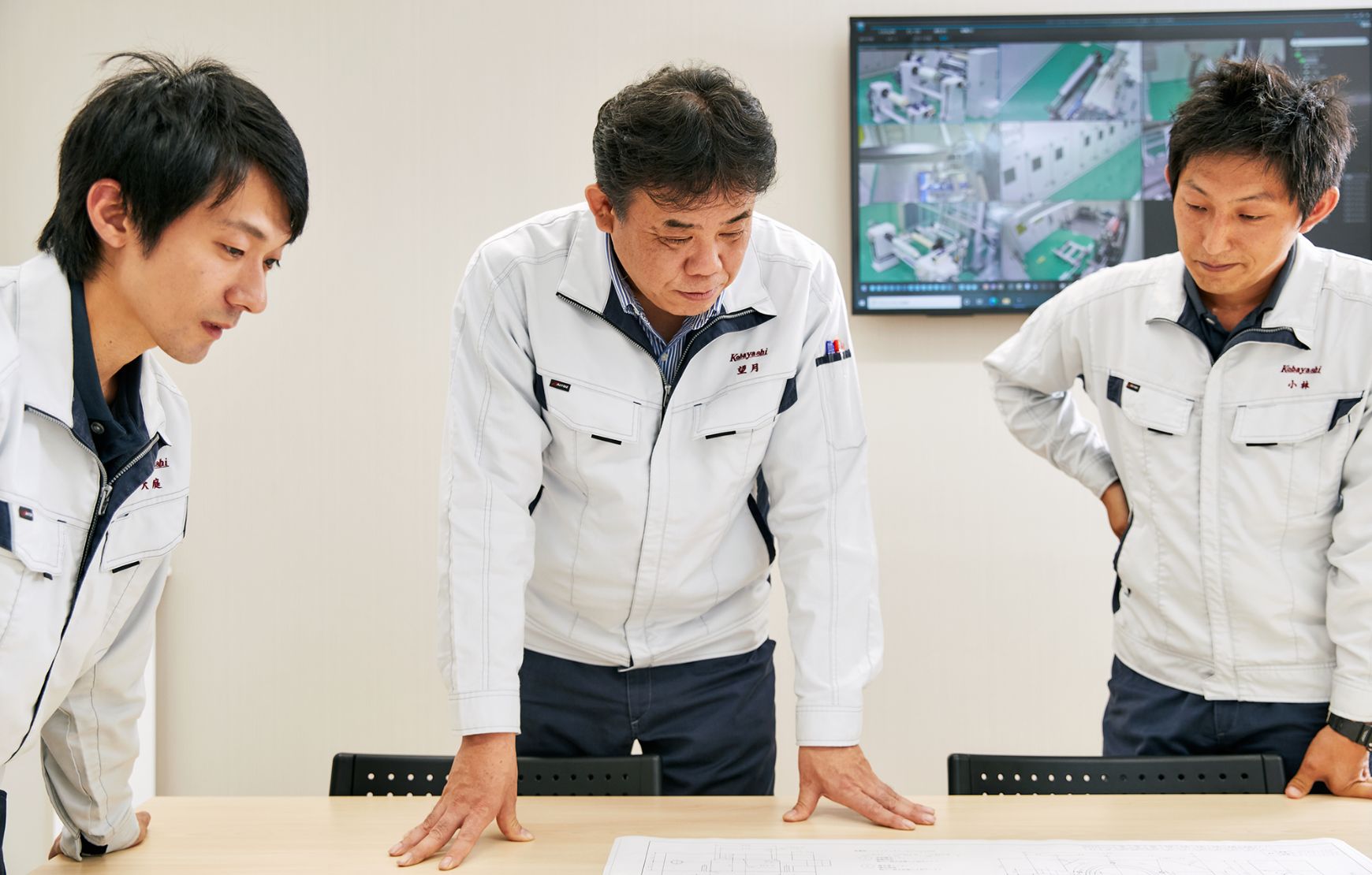
STORY・02
課題解決のヒントは「風の向き」。
トライ&エラーで見つけた
新技術開発の糸口。
課題となっているのは、乾燥の際に熱風によってフィルムがバタつき、シワが発生したり、コーティング塗料が飛散してドライヤが汚れてしまうこと。プロジェクトメンバーの一人だった小林もこれには頭を抱えていた。「テストをしているのか、掃除をしているのか途中から分からない状態になっていました。どうしようという不安やプレッシャーもありましたね。ドライヤのノズル改良を試行錯誤しながら取り組んでいたのですが、ある時掃除をしていたら“汚れ方に規則性がある”ことに気がつきました。もしかして“風の向き”がキーなんじゃないかって。」
そこから、風の流れ方にフォーカスしてノズルの改良に取り組んでいった。すると、少しずつドライヤの汚れが少なくなっていき、目に見えて改善されていくのが分かった。この時入社1年目でプロジェクトに参加していた大庭も、希望の光が見えたと語る。「一つひとつトライしてみて、汚れ方を検証するということを地道に行っていきました。1つ試すと汚れ方が変わる。一歩ずつ正解に近づいていく感覚があり、この時に製品開発の面白さを実感しましたね。」そして3ヶ月の検証の末、ようやく最適なノズルを見つけ出すことに成功した。研究開発がスタートして2年。とうとう「両面DMコータ初号機」の試運転立ち上げが韓国にて開始されたのである。
しかし、ここまではあくまで自社内にあるテスト装置での結果である。実際の装置はテスト装置の約3倍にあたる全長50mにも及ぶセパレータコーティングラインとなる。テスト装置で上手くいったからといって、実際の装置で上手くいくとは限らない。ましてやクライアントは韓国の大手有名企業。現地でプロジェクト進行に当たる望月にも失敗できないプレッシャーがのしかかる。「実際に上手く稼働するまでは不安との闘いでした。でも一つひとつ課題を解決していって、最後までやり切ったのは大きな自信につながりました。無事プロジェクトが終了したときの満足感はたまらなかったですね。」
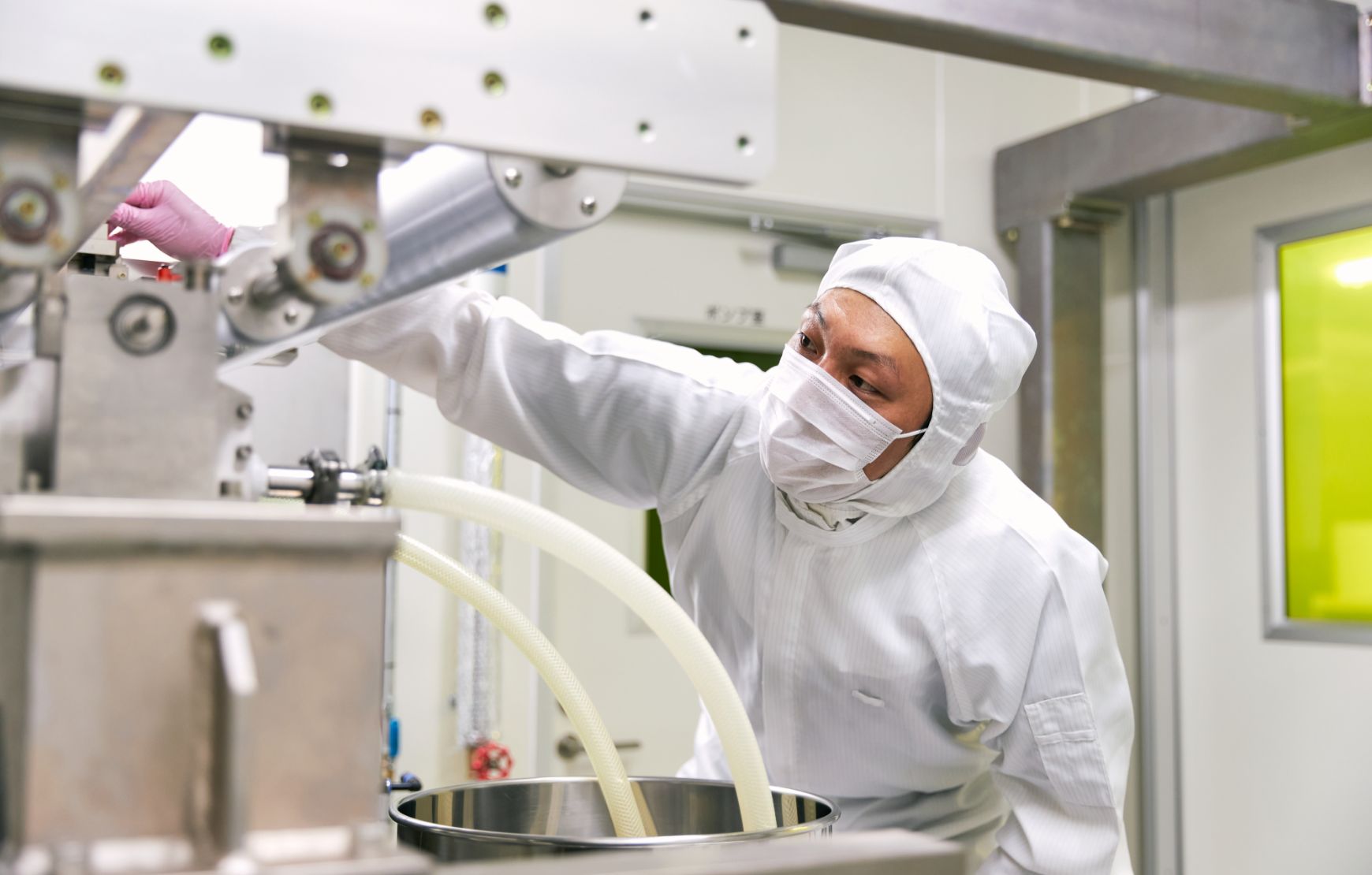
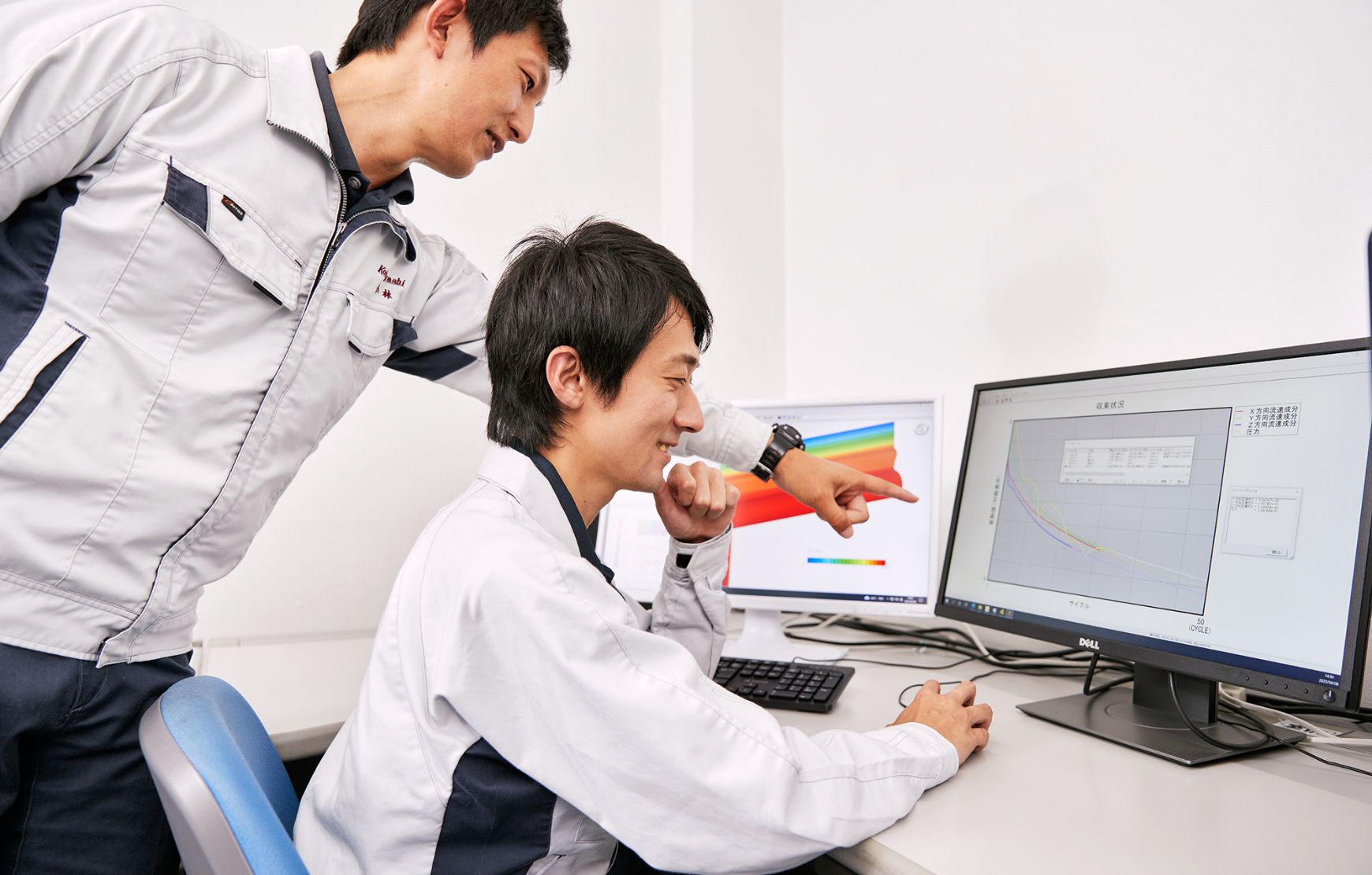
STORY・03
韓国から中国、ヨーロッパへ波及。
世界中から依頼が殺到する
ヒット商品へ。
韓国でのプロジェクト成功が口コミで広がり、2016年の中国でのプロジェクトを皮切りに、世界中から依頼が殺到することとなる。当時、中国ではEVに使用する大型のリチウムイオンバッテリーの製造が大規模に進行していた。脱炭素の観点から2035年までに市場に出される新車販売はすべてEVとなっていく。そして、リチウムイオンバッテリーを安全かつ大量に製造するには、両面コーティングができる機械が必要不可欠である。その特許技術を持っているのが小林製作所。世界中が注目するのは必然だった。
しかし、韓国で成功したからといって、他の国でも上手くいく訳ではない。中国のプロジェクトでも大きな問題が発生した。国によってフィルムや塗料の品質や性質は大きく異なるからだ。クライアントが求める製品品質をクリアするためには、これまでにない技術が要求された。課題を1つクリアすると、また次の課題がやってくる。でも、研究開発チームは諦めない。ピンチをチャンスに変え、半年以上にも及ぶ試運転の末に最適な運転条件を見つけることに成功したのである。
この中国でのプロジェクト成功から爆発的に「両面DMコータ」のニーズが拡大していくことになった。2019年にはアジアからヨーロッパへと事業フィールドが拡大。今では小林製作所の主力製品となっている。1年で5台~10台売れればヒットとなる業界で、約10年で350台以上の販売台数を記録していることからも、その圧倒的な成長スピードが伺える。だが、技術に終わりはない。研究開発部はさらなる生産速度の高速化に向けて日々改良を重ねている。小林製作所が見つめているのは未来だ。技術の発展のため、世界中の人々が快適に暮らせる社会のため、生活に役立つモノづくりにこれからも挑戦し続ける。
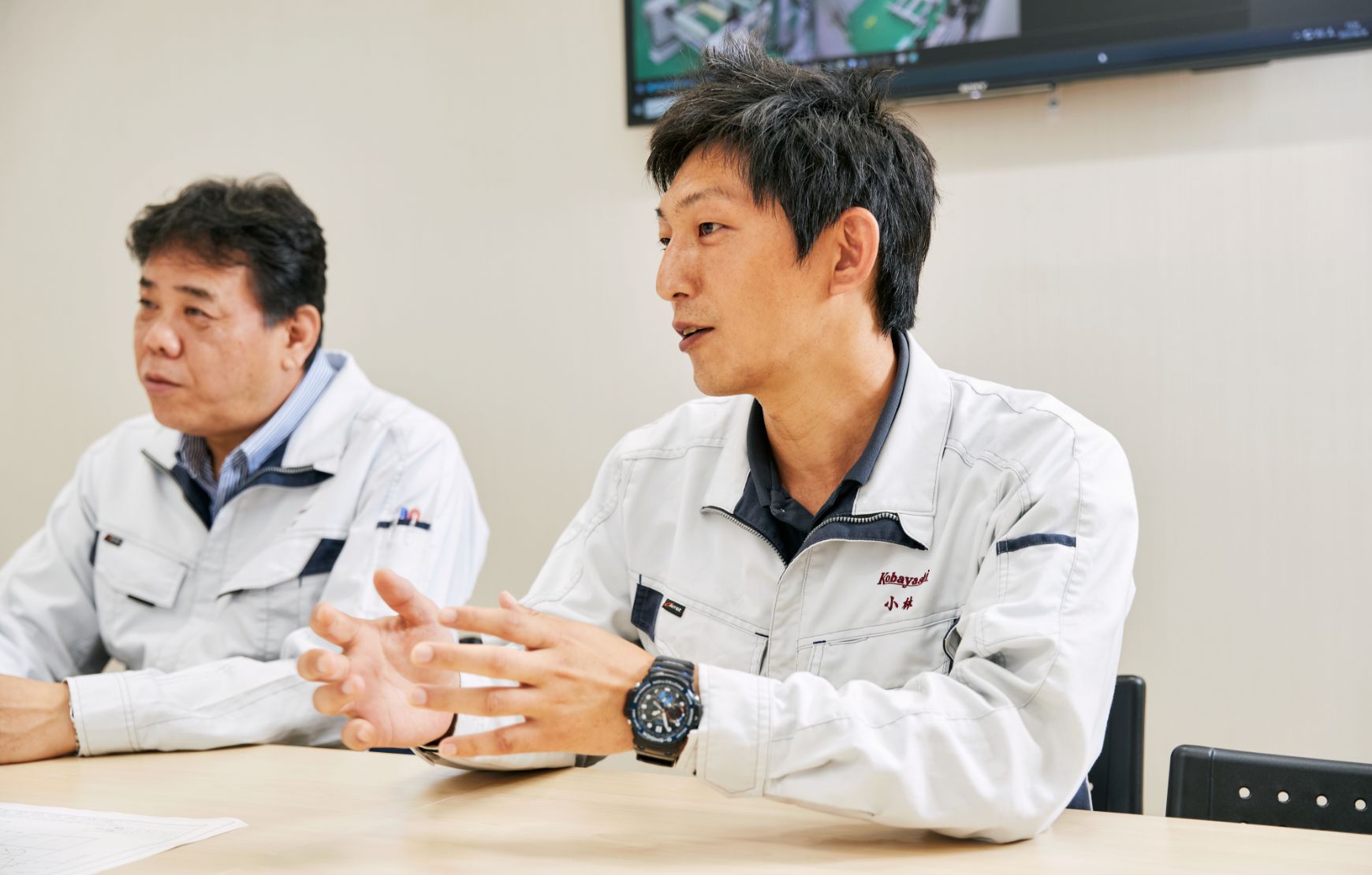
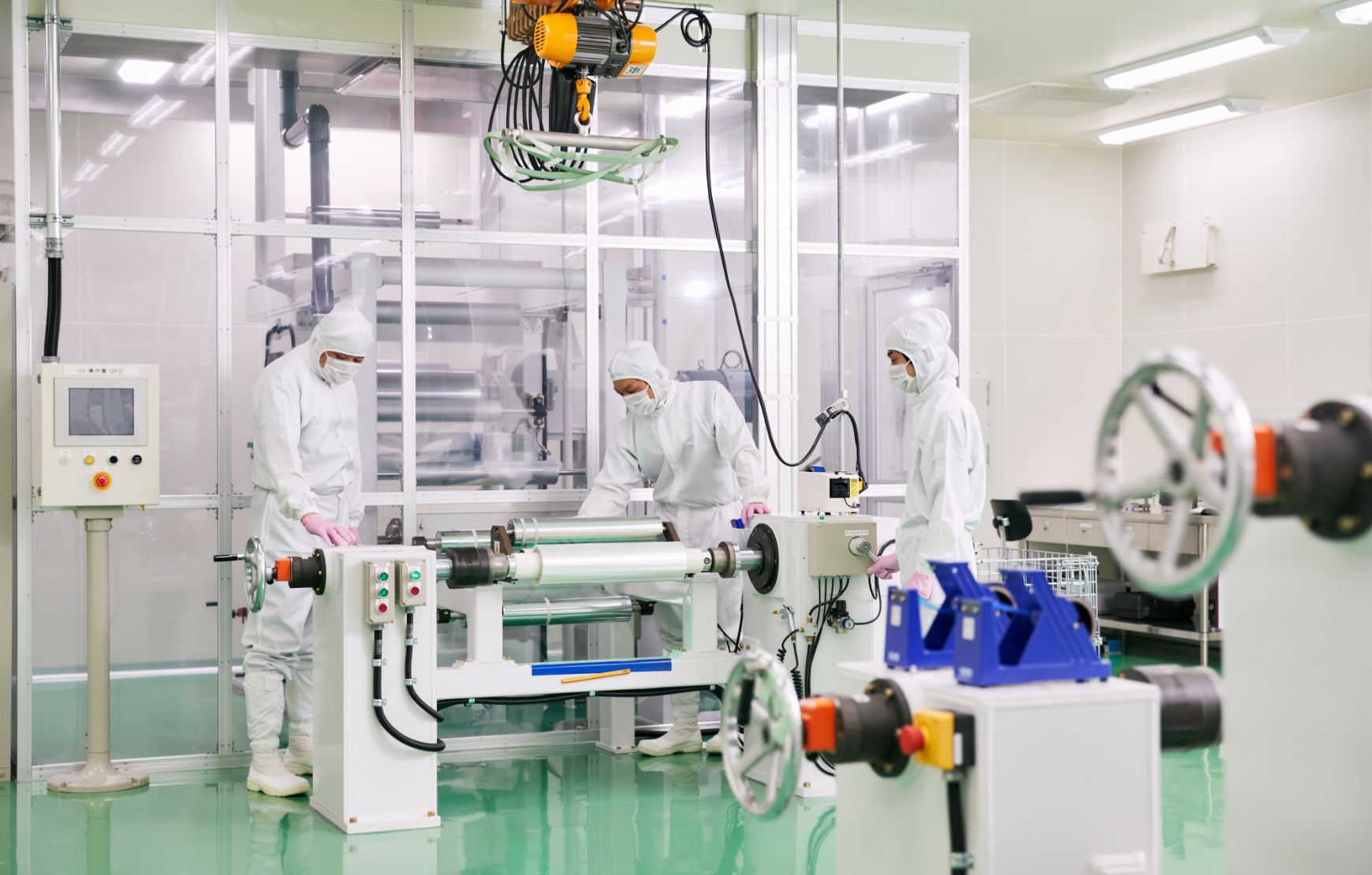
AFTER TALK
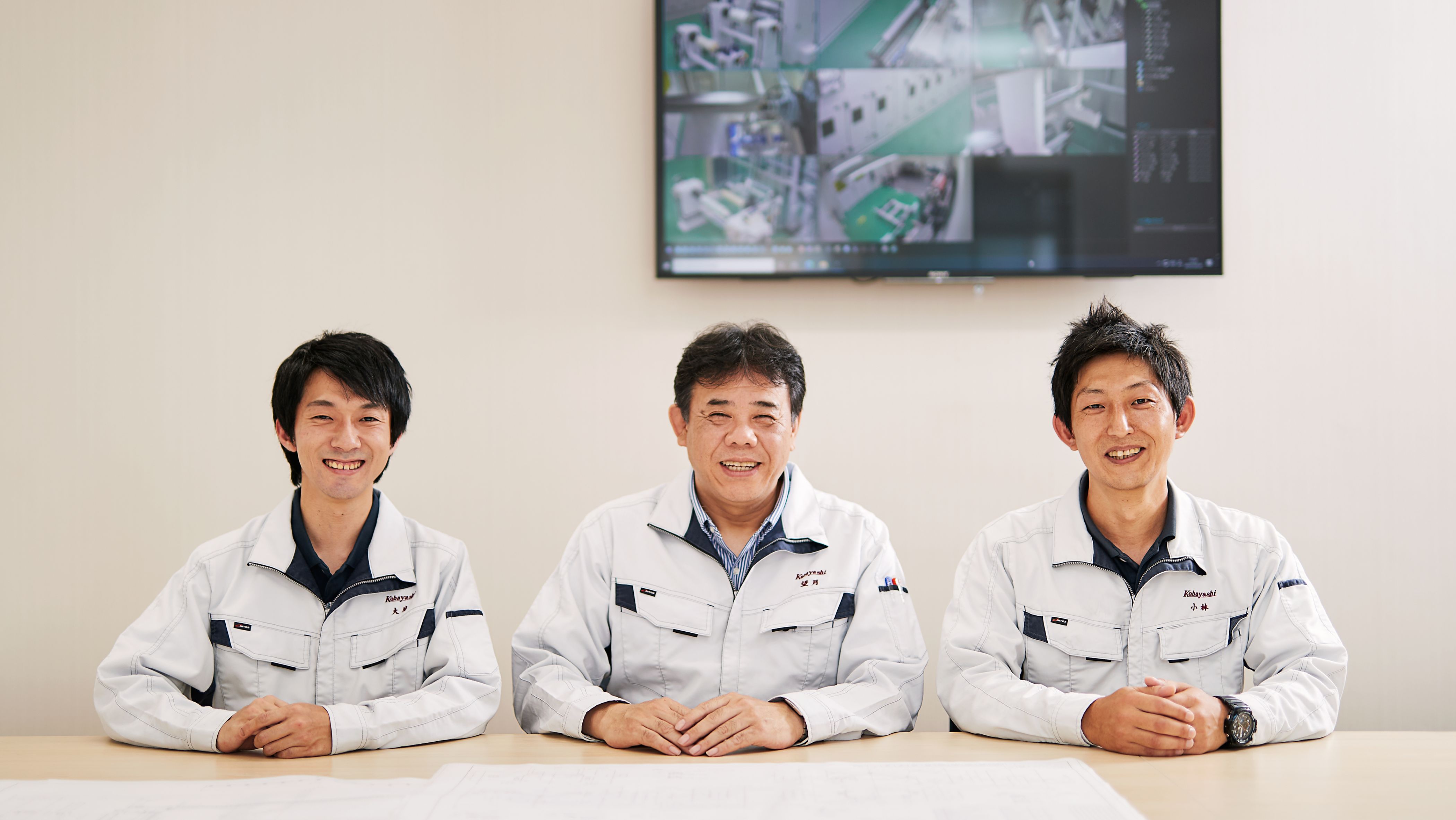
小林(写真・右):2012年の韓国のプロジェクトの時は、本当に大変でしたね。途中、ノズルの掃除ばかりしていました。でも、そのおかげで解決のヒントが見つかりました。
望月(写真・中央):この経験を通して、今ではコンピューターで風の流れをシミュレーションする「流体解析」が導入されることになって、その専任者に抜擢されたのが、大庭さん。イチから勉強して計算力学技術者の資格も取得したのはすごいことですよ。
大庭(写真・左):ありがとうございます。最初は本当に手探りでした。約2年、コンピューターシミュレーションと実際のテスト結果の整合性を検証して、やっと実務にも活用できるようになりました。でも、本当にシミュレーション通りに行くか、いつもドキドキしていますね。
望月:この流体解析が導入されたおかげで、韓国のプロジェクトの時のように何度もテストを繰り返す必要がなくなって、大幅な時間とコストの削減につながりました。今では小林製作所に欠かせない開発ツールになっていますよ。大庭さん、ありがとう!